Magnetic Components for Motors
As a manufacturer of permanent magnets, we not only produce and sell magnets, but also provide a complete set of magnetic assembly services. In many cases, the components need to be machined or electroplated after the magnets are installed. At this time, it is particularly important to hand over the product to us for installation. A complete magnetic assembly usually consists of several parts, and the processing and assembly process of the magnet is completely different from other metal parts. Product accuracy, magnetic circuit during assembly, equipment adjustment during processing, etc., are all key factors that determine the accuracy and pass rate of the finished product.
The following are the products and services we provide for permanent magnet synchronous motors:
1. Permanent magnets
Neodymium-Iron-Boron (NdFeB) Magnets
Known for its high energy product, strong magnetic performance, and high remanence. However, NdFeB magnets can be sensitive to high temperatures and may require coatings to prevent corrosion. These are often used in applications where high power density is required.
Samarium Cobalt (SmCo) Magnets
Offers good magnetic properties and has better temperature stability than NdFeB, making it suitable for high-temperature environments (up to 300°C). It is also corrosion-resistant, but more expensive.
AlNiCo Magnets
AlNiCo magnets has lower coercivity but offers excellent temperature stability. AlNiCo magnets are suitable for applications with less risk of demagnetization but extreme temperatures.
Ferrite Magnets
Ferrite magnets are widely used for cost-effective applications. They have lower magnetic strength compared to rare-earth magnets but are inexpensive and perform well in low to moderate temperature conditions.
2. Permanent Magnet Rotor For PMSM
A permanent magnet rotor is a key component of a permanent magnet motor (PM motor), responsible for producing the motor’s rotating magnetic field.
There are two common types based on how the magnets are placed within or on the rotor:
Surface-Mounted Permanent Magnet (SPM) Rotors
The magnets are mounted on the surface of the rotor.
SPM designs are simpler to manufacture and offer high torque density.
These motors are generally less expensive than interior magnet types.
However, the magnets in SPM motors are more exposed, leading to higher risks of demagnetization under high-speed operation or high temperature.
Interior Permanent Magnet (IPM) Rotors
In IPM designs, the magnets are embedded within the rotor core.
This configuration offers better protection for the magnets, improving resistance to demagnetization.
IPM rotors also allow for field-weakening control (to operate efficiently at higher speeds) and often have better mechanical stability at high speeds.
However, they are more complex and expensive to manufacture.
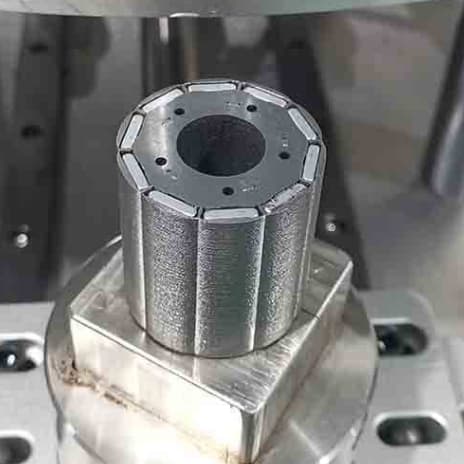
3. Permanent Magnet Rotor for Disk Motor
A disk motor with a permanent magnet rotor is a type of electric motor characterized by its compact design and flat, disk-like structure. This configuration is particularly advantageous in applications requiring high torque and efficiency in a small form factor. Disk Motor Permanent Magnet Rotor is typically a flat, disk-shaped component that houses permanent magnets arranged in a circular pattern. This design allows for a larger surface area for magnetic interaction with the stator.
There are two types of Permanent Magnet Configurations
-
Surface-Mounted Magnets
In this design, magnets are affixed to the surface of the rotor. This configuration is simpler and allows for easier manufacturing but may have limitations in terms of thermal stability and susceptibility to demagnetization.
-
Embedded Magnets
Magnets are placed inside the rotor material, providing better protection and improving thermal performance. This arrangement can enhance demagnetization resistance and is commonly found in higher-performance applications.
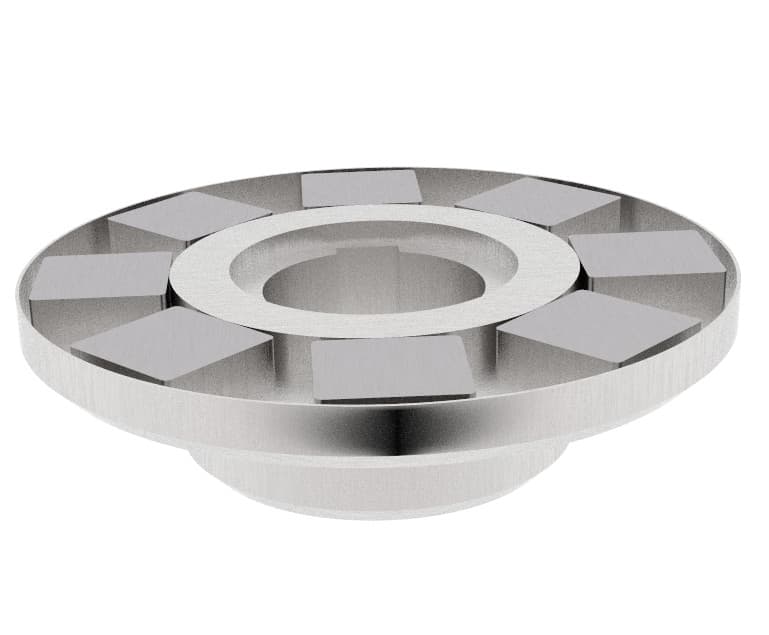
4. Permanent Magnet Rotor for Linear Motor
A linear motor with a permanent magnet rotor functions differently from conventional rotary motors. In a linear motor, the rotor (also known as the forcer in linear motor terminology) and stator are “unrolled” so that instead of producing rotational motion, the motor generates linear motion directly. This is especially useful in applications requiring precise, smooth, and fast linear movements.The rotor contains permanent magnets arranged in a linear configuration, either on the surface or embedded inside.
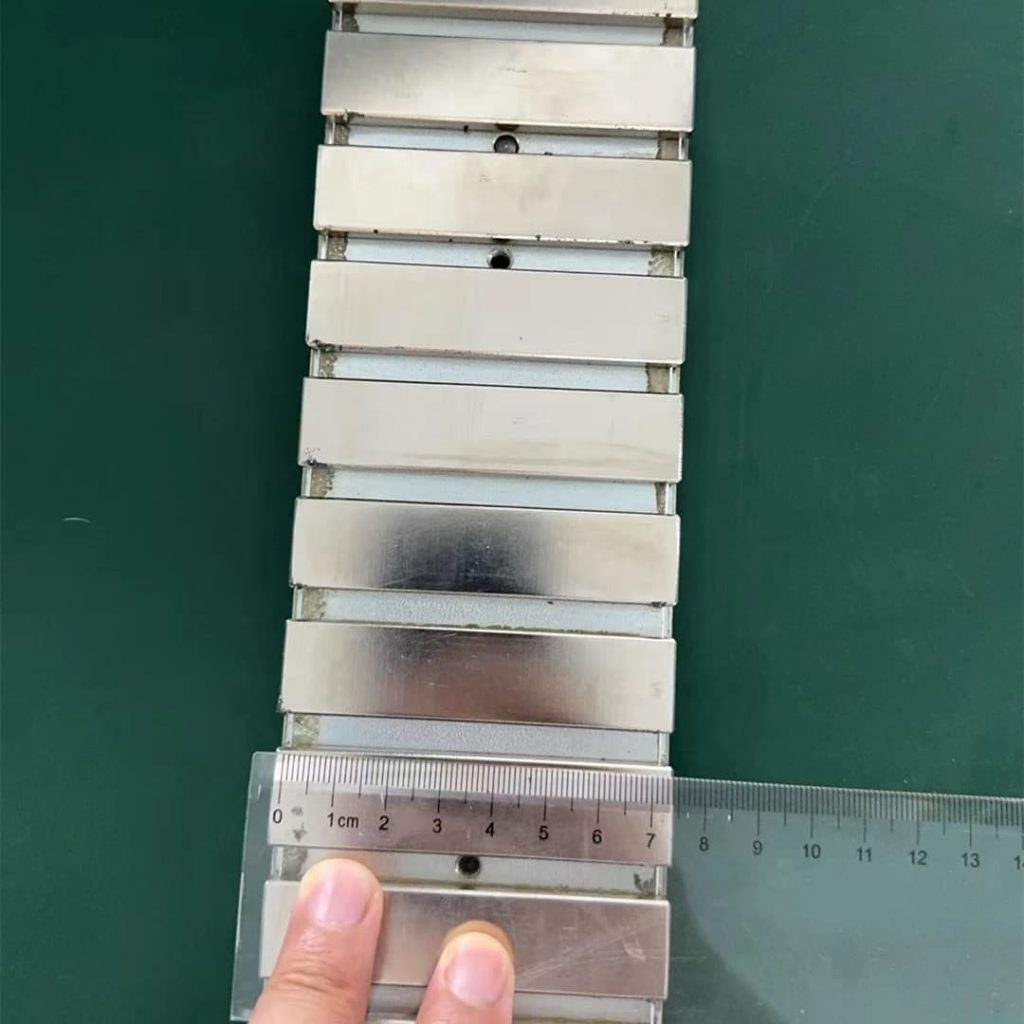