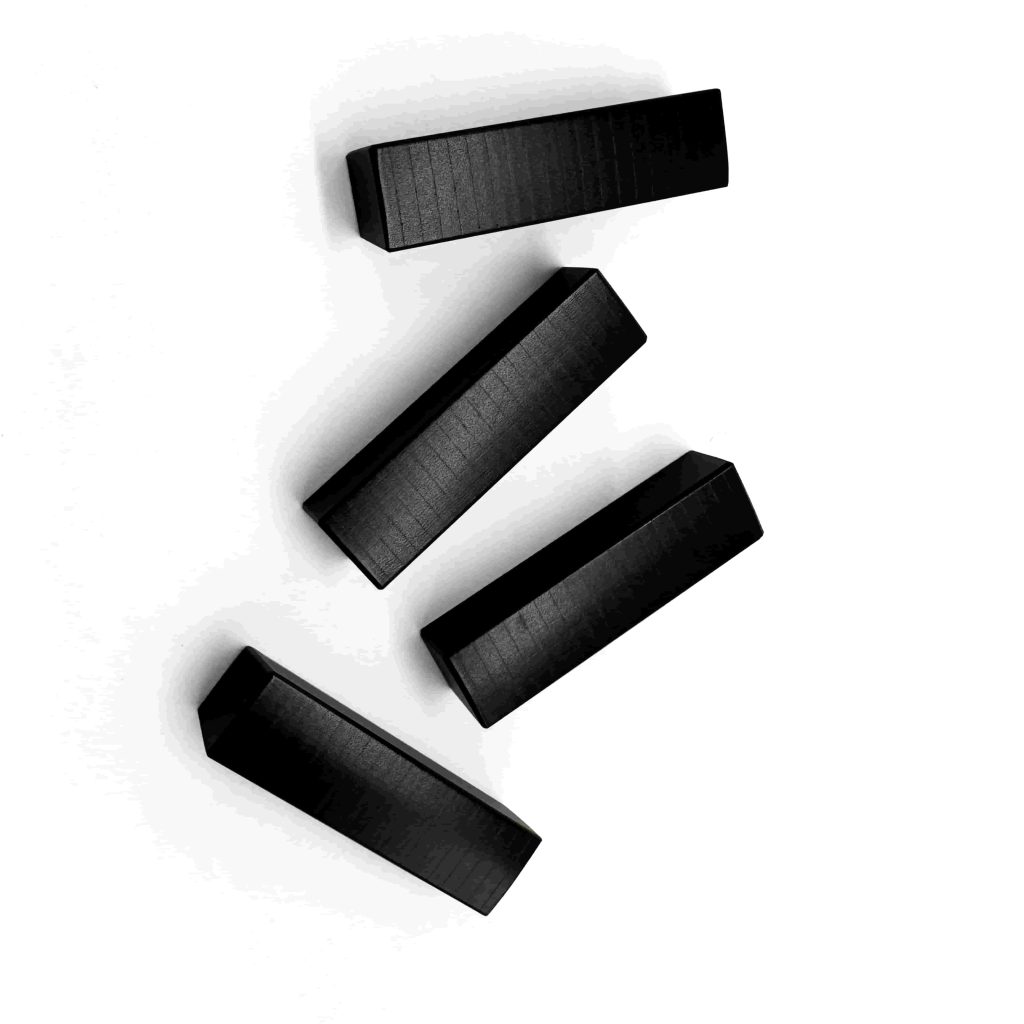
Laminated Magnets-The right way for solving eddy effect
Laminated magnets are a type of magnets designed to reduce energy losses and improve efficiency in electrical devices. They are essentially magnets made by stacking thin layers, or lamination, of magnetic material together. Each layer is typically coated with an insulating material to prevent electrical currents from flowing between them.
The primary advantage of laminating magnets is to minimize eddy current losses. Eddy currents are loops of electrical current that can form within conductors when they are exposed to a changing magnetic field. These currents generate heat and waste energy. By laminating the magnetic material, the eddy currents are confined to each thin layer, and the insulating coatings prevent them from flowing between layers. This results in a more efficient magnetic field with less energy lost as heat.
Laminated magnets are commonly used in applications where magnetic fields are rapidly changing, such as in electric motors, transformers, and generators. They help enhance the performance and longevity of these devices by improving energy efficiency and reducing heat generation.